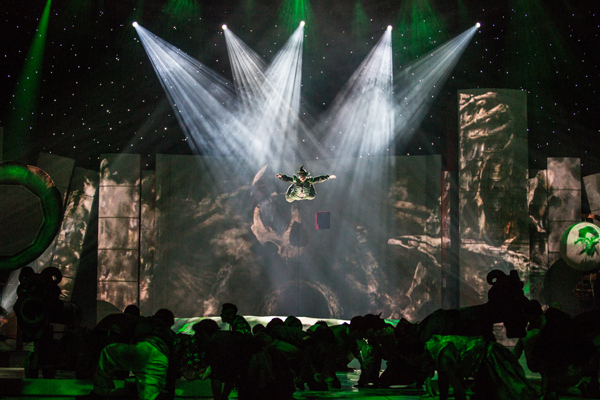
Peter Pan - Luc Petit Creation
To create and make a dress worn by an athlete who doubled for the singer and who appeared above a wind machine with a wind velocity of over 250 Km / h.
The dress, fluid and light, was a copy of the singer's but was an all-in-one piece with concealed features so it could meet this technical challenge. It included gussets to slow it down and flounces to maintain its’ stability. The material chosen was a technical fabric able to withstand the power of the wind machine and to protect the athlete. Finally, seams were placed at strategic points to stop the fabric tearing.
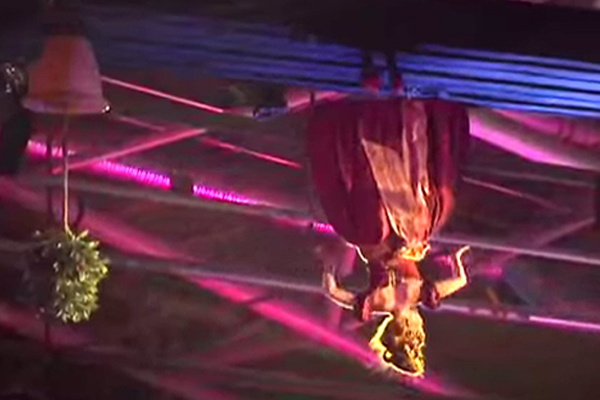
«The enchanted castle» Luc Petit Creation
To create and design a dress for a Marchioness worn by a performer who had to appear to the audience upside down on the ceiling above the stage.
Flexible and rigid, the dress allowed the artist to perform in this position without any piece of fabric or ribbon falling off during her performance. Thanks to the choice of materials and their technical nature, she could change by herself, upside down, in a tiny black box that served as a dressing room up on high, and put on under the dress all the technical equipment necessary to ensure her safety during her performance.
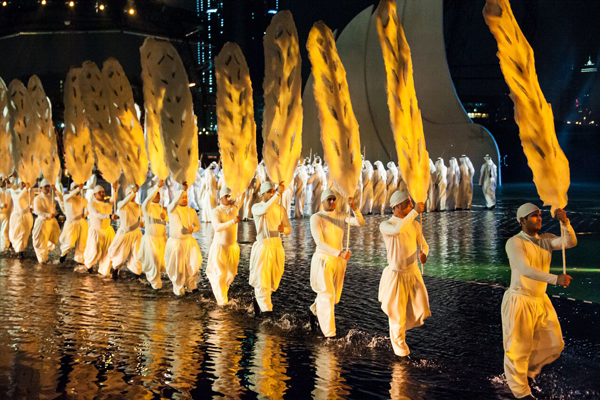
44th UAE National Day Dubaï, Emirates
Bringing out everyone’s skills and sharing them to get the best from them in a very short time.
Design and production of 6 different types of accessories, the key elements of the show, with between 20 and 65 examples made of each, within 30 days before the show. In order to respect delivery deadlines, the accessories designs were adapted according to materials already in stock or purchased locally. Manufacturing techniques were selected based on skills of the teams on site to save time and thus deliver the accessories at the earliest possible date so that the performers could rehearse with them and make the final adjustments.
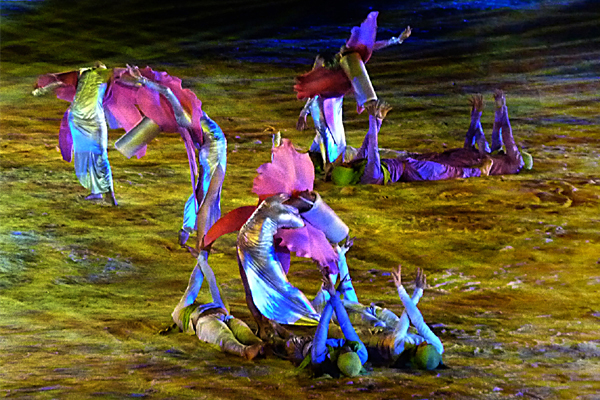
IX South American games Medellin, Colombia
Meeting a tight budget that required managing the long distance production of costumes with only 3 months of preparation and three short trips there.
A locally recruited assistant managed all the plants needed for the production of the collection. A pilot workshop was created for the production of individual pieces as well as collections of 3 to 5 pieces and it involved local Medellin seamstresses. In order to respect delivery deadlines and allow performers to rehearse with their costumes, materials were purchased locally and manufacturing techniques were adapted to the teams’ skills.
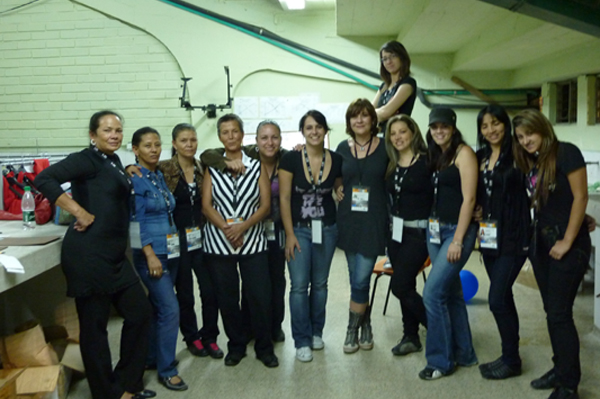
IX South American games Medellin, Colombia
Taking a sewing team beyond what they can imagine.
The project was completed thanks to the union and solidarity of the team which reached its peak during the preparation of the show. Seeing the joy and pride in the eyes of each person involved is the greatest reward one can have. This too is the mark of a successful project.
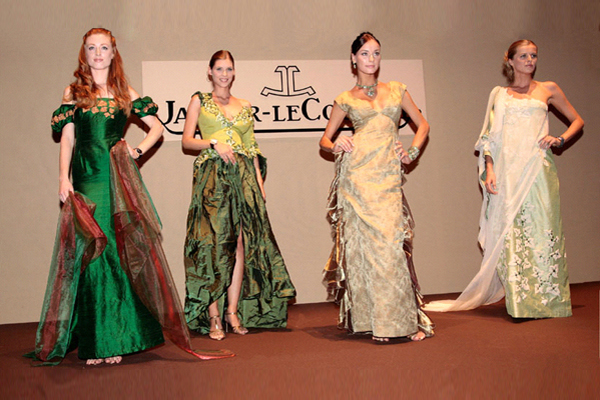
« Le Lierre » Jaeger LeCoultre - Venice, Italy